Filter Results
Related Organization
- Biological and Environmental Systems Science Directorate (23)
- Computing and Computational Sciences Directorate (35)
- Energy Science and Technology Directorate (217)
- Fusion and Fission Energy and Science Directorate (21)
- Information Technology Services Directorate (2)
- Isotope Science and Enrichment Directorate (6)
- National Security Sciences Directorate (17)
- Neutron Sciences Directorate (11)
- Physical Sciences Directorate (128)
- User Facilities (27)
Researcher
- Chris Tyler
- Justin West
- Ritin Mathews
- David Olvera Trejo
- Hongbin Sun
- J.R. R Matheson
- Jaydeep Karandikar
- Prashant Jain
- Scott Smith
- Akash Jag Prasad
- Alexander I Wiechert
- Andrew F May
- Ben Garrison
- Benjamin Manard
- Brad Johnson
- Brandon A Wilson
- Brian Gibson
- Brian Post
- Calen Kimmell
- Callie Goetz
- Charles F Weber
- Christopher Hobbs
- Costas Tsouris
- Eddie Lopez Honorato
- Emma Betters
- Fred List III
- Govindarajan Muralidharan
- Greg Corson
- Hsin Wang
- Ian Greenquist
- Ilias Belharouak
- Isaac Sikkema
- Jesse Heineman
- Joanna Mcfarlane
- John Potter
- Jonathan Willocks
- Joseph Olatt
- Josh B Harbin
- Keith Carver
- Kunal Mondal
- Mahim Mathur
- Matt Kurley III
- Matt Vick
- Mike Zach
- Mingyan Li
- Nate See
- N Dianne Ezell
- Nedim Cinbiz
- Nithin Panicker
- Oscar Martinez
- Pradeep Ramuhalli
- Praveen Cheekatamarla
- Richard Howard
- Rodney D Hunt
- Rose Montgomery
- Ruhul Amin
- Ryan Heldt
- Sam Hollifield
- Thomas Butcher
- Thomas R Muth
- Tony L Schmitz
- Tyler Gerczak
- Ugur Mertyurek
- Vandana Rallabandi
- Venugopal K Varma
- Vishaldeep Sharma
- Vittorio Badalassi
- Vladimir Orlyanchik
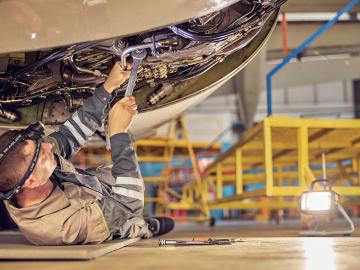
Materials produced via additive manufacturing, or 3D printing, can experience significant residual stress, distortion and cracking, negatively impacting the manufacturing process.
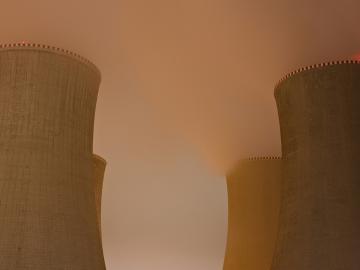
Currently there is no capability to test materials, sensors, and nuclear fuels at extremely high temperatures and under radiation conditions for nuclear thermal rocket propulsion or advanced reactors.
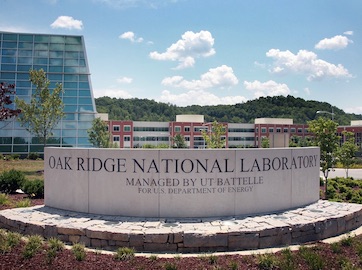
Quantifying tool wear is historically challenging task due to variable human interpretation. This capture system will allow for an entire side and the complete end of the cutting tool to be analyzed.
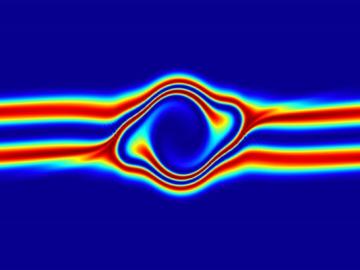
Recent advances in magnetic fusion (tokamak) technology have attracted billions of dollars of investments in startups from venture capitals and corporations to develop devices demonstrating net energy gain in a self-heated burning plasma, such as SPARC (under construction) and
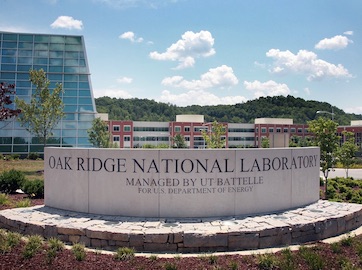
ORNL will develop an advanced high-performing RTG using a novel radioisotope heat source.
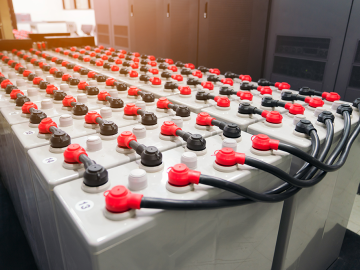
Knowing the state of charge of lithium-ion batteries, used to power applications from electric vehicles to medical diagnostic equipment, is critical for long-term battery operation.
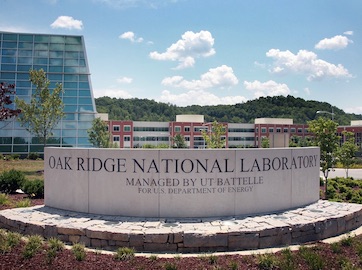
The use of Fluidized Bed Chemical Vapor Deposition to coat particles or fibers is inherently slow and capital intensive, as it requires constant modifications to the equipment to account for changes in the characteristics of the substrates to be coated.
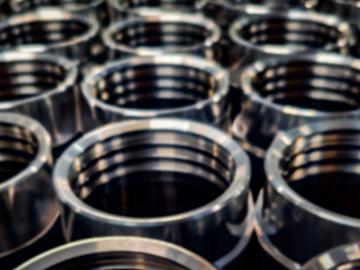
Complex protective casings and housings are necessary for many applications, including combustion chambers of gas turbines used in aerospace engines. Manufacturing these components from forging and/or casting as a whole is challenging, costly, and time-consuming.

Real-time tracking and monitoring of radioactive/nuclear materials during transportation is a critical need to ensure safety and security. Current technologies rely on simple tagging, using sensors attached to transport containers, but they have limitations.