Filter Results
Related Organization
- Biological and Environmental Systems Science Directorate (23)
- Computing and Computational Sciences Directorate (35)
- Energy Science and Technology Directorate (217)
- Fusion and Fission Energy and Science Directorate (21)
- Information Technology Services Directorate (2)
- Isotope Science and Enrichment Directorate (6)
- National Security Sciences Directorate (17)
- Neutron Sciences Directorate (11)
- Physical Sciences Directorate (128)
- User Facilities (27)
Researcher
- Chris Tyler
- Justin West
- Ritin Mathews
- Singanallur Venkatakrishnan
- Venugopal K Varma
- Amir K Ziabari
- David Olvera Trejo
- Diana E Hun
- J.R. R Matheson
- Jaydeep Karandikar
- Mahabir Bhandari
- Philip Bingham
- Philip Boudreaux
- Ryan Dehoff
- Scott Smith
- Stephen M Killough
- Vincent Paquit
- Adam Aaron
- Akash Jag Prasad
- Brian Gibson
- Brian Post
- Bryan Maldonado Puente
- Calen Kimmell
- Charles D Ottinger
- Corey Cooke
- Emma Betters
- Gina Accawi
- Govindarajan Muralidharan
- Greg Corson
- Gurneesh Jatana
- Jesse Heineman
- John Potter
- Josh B Harbin
- Mark M Root
- Michael Kirka
- Nolan Hayes
- Obaid Rahman
- Peter Wang
- Rose Montgomery
- Ryan Kerekes
- Sally Ghanem
- Sergey Smolentsev
- Thomas R Muth
- Tony L Schmitz
- Vladimir Orlyanchik
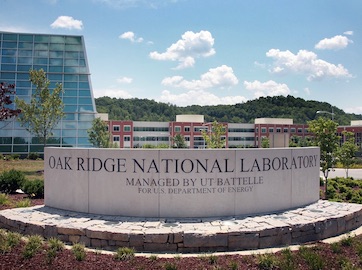
ORNL researchers have developed a deep learning-based approach to rapidly perform high-quality reconstructions from sparse X-ray computed tomography measurements.
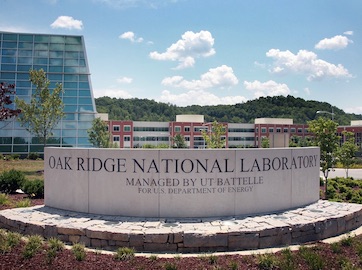
System and method for part porosity monitoring of additively manufactured components using machining
In additive manufacturing, choice of process parameters for a given material and geometry can result in porosities in the build volume, which can result in scrap.
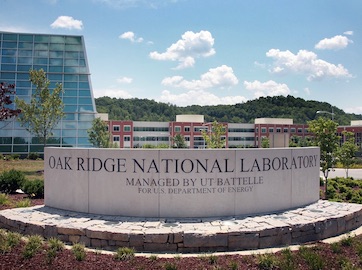
We have been working to adapt background oriented schlieren (BOS) imaging to directly visualize building leakage, which is fast and easy.
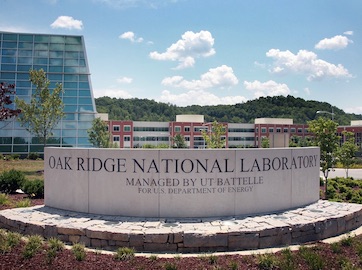
Distortion generated during additive manufacturing of metallic components affect the build as well as the baseplate geometries. These distortions are significant enough to disqualify components for functional purposes.
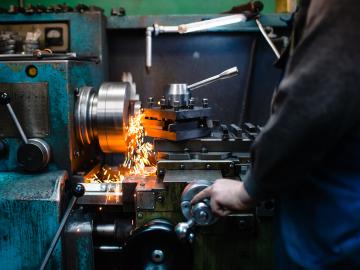
For additive manufacturing of large-scale parts, significant distortion can result from residual stresses during deposition and cooling. This can result in part scraps if the final part geometry is not contained in the additively manufactured preform.
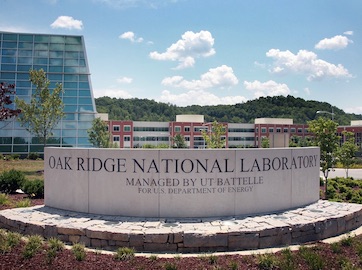
In additive manufacturing large stresses are induced in the build plate and part interface. A result of these stresses are deformations in the build plate and final component.
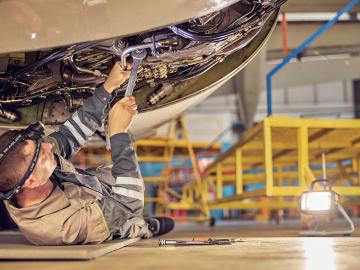
Materials produced via additive manufacturing, or 3D printing, can experience significant residual stress, distortion and cracking, negatively impacting the manufacturing process.
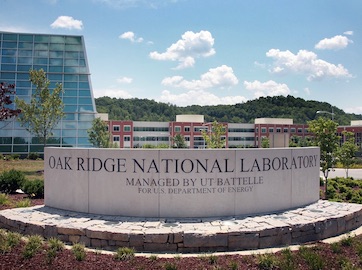
Fusion reactors need efficient systems to create tritium fuel and handle intense heat and radiation. Traditional liquid metal systems face challenges like high pressure losses and material breakdown in strong magnetic fields.
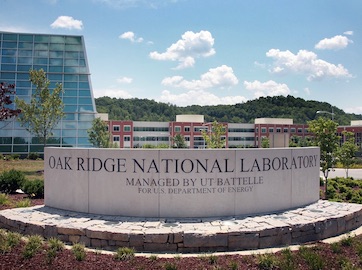
The traditional window installation process involves many steps. These are becoming even more complex with newer construction requirements such as installation of windows over exterior continuous insulation walls.