Filter Results
Related Organization
- Biological and Environmental Systems Science Directorate (29)
- Computing and Computational Sciences Directorate (39)
- Energy Science and Technology Directorate (229)
- Fusion and Fission Energy and Science Directorate
(24)
- Information Technology Services Directorate (3)
- National Security Sciences Directorate (20)
- Neutron Sciences Directorate (11)
- Physical Sciences Directorate (138)
- User Facilities (28)
- (-) Isotope Science and Enrichment Directorate (7)
Researcher
- Chris Tyler
- Justin West
- Ritin Mathews
- Hongbin Sun
- David Olvera Trejo
- J.R. R Matheson
- Jaydeep Karandikar
- Mike Zach
- Prashant Jain
- Scott Smith
- Akash Jag Prasad
- Andrew F May
- Annetta Burger
- Ben Garrison
- Brad Johnson
- Brian Gibson
- Brian Post
- Bruce Moyer
- Calen Kimmell
- Carter Christopher
- Chance C Brown
- Charlie Cook
- Christopher Hershey
- Craig Blue
- Daniel Rasmussen
- Debjani Pal
- Debraj De
- Emma Betters
- Gautam Malviya Thakur
- Greg Corson
- Hsin Wang
- Ian Greenquist
- Ilias Belharouak
- James Gaboardi
- James Klett
- Jeffrey Einkauf
- Jennifer M Pyles
- Jesse Heineman
- Jesse McGaha
- John Lindahl
- John Potter
- Josh B Harbin
- Justin Griswold
- Kevin Sparks
- Kuntal De
- Laetitia H Delmau
- Liz McBride
- Luke Sadergaski
- Nate See
- Nedim Cinbiz
- Nithin Panicker
- Padhraic L Mulligan
- Pradeep Ramuhalli
- Praveen Cheekatamarla
- Ruhul Amin
- Sandra Davern
- Thien D. Nguyen
- Todd Thomas
- Tony Beard
- Tony L Schmitz
- Vishaldeep Sharma
- Vittorio Badalassi
- Vladimir Orlyanchik
- Xiuling Nie
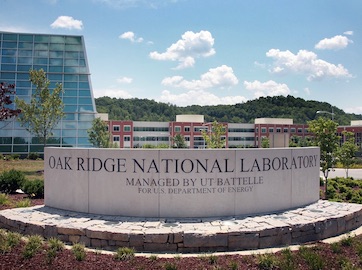
In nuclear and industrial facilities, fine particles, including radioactive residues—can accumulate on the interior surfaces of ventilation ducts and equipment, posing serious safety and operational risks.
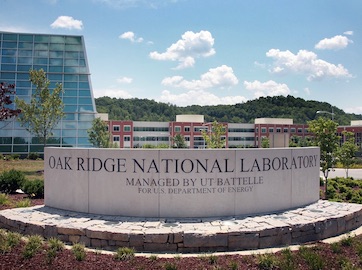
Often there are major challenges in developing diverse and complex human mobility metrics systematically and quickly.
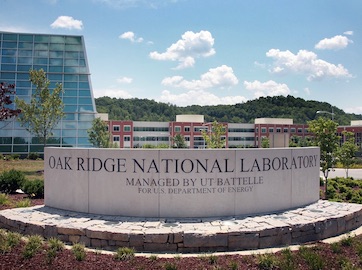
Ruthenium is recovered from used nuclear fuel in an oxidizing environment by depositing the volatile RuO4 species onto a polymeric substrate.
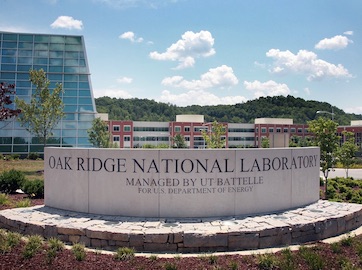
System and method for part porosity monitoring of additively manufactured components using machining
In additive manufacturing, choice of process parameters for a given material and geometry can result in porosities in the build volume, which can result in scrap.
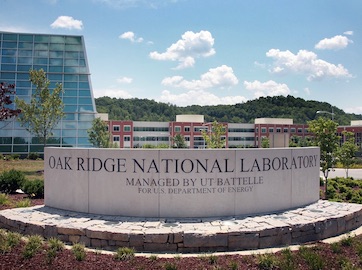
The invention presented here addresses key challenges associated with counterfeit refrigerants by ensuring safety, maintaining system performance, supporting environmental compliance, and mitigating health and legal risks.
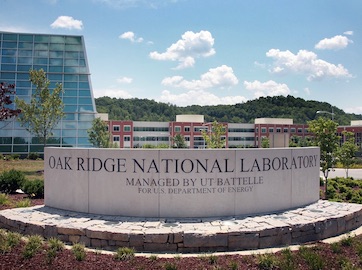
Distortion generated during additive manufacturing of metallic components affect the build as well as the baseplate geometries. These distortions are significant enough to disqualify components for functional purposes.
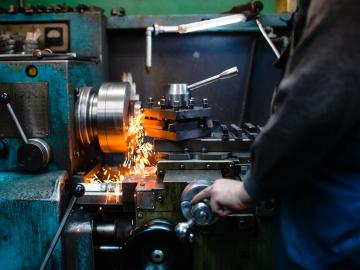
For additive manufacturing of large-scale parts, significant distortion can result from residual stresses during deposition and cooling. This can result in part scraps if the final part geometry is not contained in the additively manufactured preform.
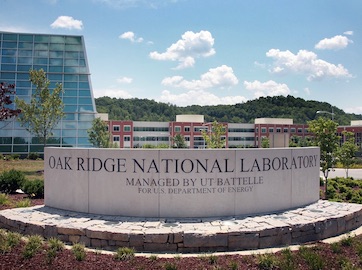
A novel approach is presented herein to improve time to onset of natural convection stemming from fuel element porosity during a failure mode of a nuclear reactor.
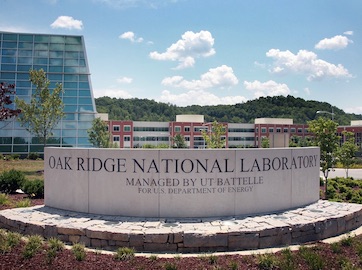
In additive manufacturing large stresses are induced in the build plate and part interface. A result of these stresses are deformations in the build plate and final component.