Filter Results
Related Organization
- Biological and Environmental Systems Science Directorate (29)
- Computing and Computational Sciences Directorate (39)
- Energy Science and Technology Directorate (229)
- Fusion and Fission Energy and Science Directorate (24)
- Information Technology Services Directorate (3)
- Isotope Science and Enrichment Directorate (7)
- National Security Sciences Directorate (20)
- Neutron Sciences Directorate (11)
- Physical Sciences Directorate (138)
- User Facilities (28)
Researcher
- Steve Bullock
- Chris Tyler
- Corson Cramer
- Justin West
- Ritin Mathews
- Ahmed Hassen
- Greg Larsen
- James Klett
- Nadim Hmeidat
- Srikanth Yoginath
- Trevor Aguirre
- Vlastimil Kunc
- David Olvera Trejo
- J.R. R Matheson
- James J Nutaro
- Jaydeep Karandikar
- Pratishtha Shukla
- Scott Smith
- Steven Guzorek
- Sudip Seal
- Akash Jag Prasad
- Ali Passian
- Beth L Armstrong
- Brian Gibson
- Brian Post
- Brittany Rodriguez
- Calen Kimmell
- Charlie Cook
- Christopher Hershey
- Christopher Ledford
- Craig Blue
- Dan Coughlin
- Daniel Rasmussen
- David J Mitchell
- David Nuttall
- Dustin Gilmer
- Emma Betters
- Greg Corson
- Harper Jordan
- Jesse Heineman
- Joel Asiamah
- Joel Dawson
- John Lindahl
- John Potter
- Jordan Wright
- Josh B Harbin
- Michael Kirka
- Nance Ericson
- Sana Elyas
- Subhabrata Saha
- Tomonori Saito
- Tony Beard
- Tony L Schmitz
- Tyler Smith
- Varisara Tansakul
- Vipin Kumar
- Vladimir Orlyanchik
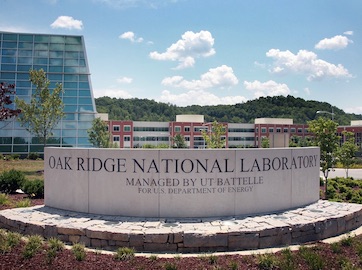
The technology will offer supportless DIW of complex structures using vinyl ester resin, facilitated by multidirectional 6 axis printing.
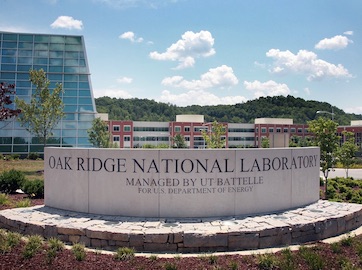
The technologies provide additively manufactured thermal protection system.
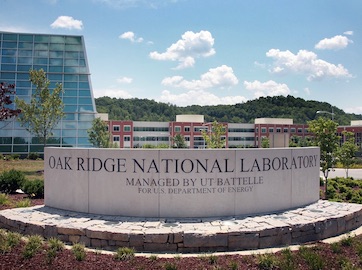
System and method for part porosity monitoring of additively manufactured components using machining
In additive manufacturing, choice of process parameters for a given material and geometry can result in porosities in the build volume, which can result in scrap.
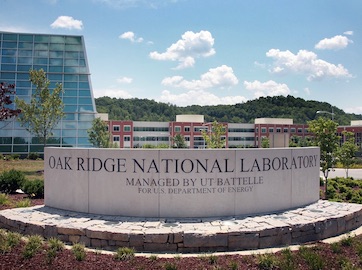
Reflective and emissive surfaces are designed with heat retention as opposed to the current state of the art oven and furnaces which use non-reflective surfaces. Heat is absorbed and transferred to the exterior of the heated appliances.
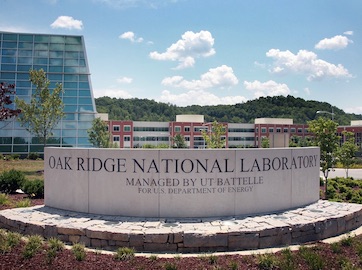
This invention focuses on improving the ceramic yield of preceramic polymers by tuning the crosslinking process that occurs during vat photopolymerization (VP).
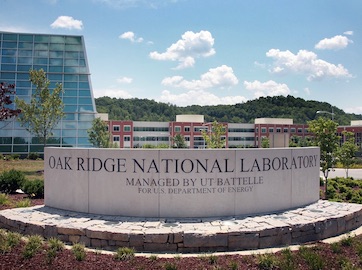
Distortion generated during additive manufacturing of metallic components affect the build as well as the baseplate geometries. These distortions are significant enough to disqualify components for functional purposes.
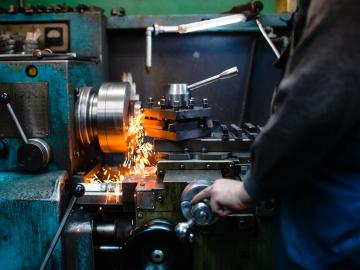
For additive manufacturing of large-scale parts, significant distortion can result from residual stresses during deposition and cooling. This can result in part scraps if the final part geometry is not contained in the additively manufactured preform.
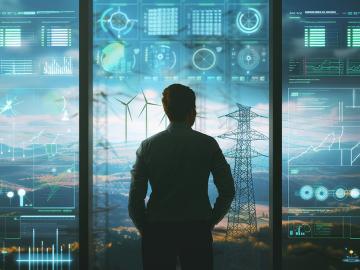
Digital twins (DTs) have emerged as essential tools for monitoring, predicting, and optimizing physical systems by using real-time data.
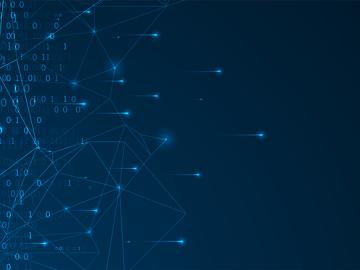
Simulation cloning is a technique in which dynamically cloned simulations’ state spaces differ from their parent simulation due to intervening events.