Filter Results
Related Organization
- Biological and Environmental Systems Science Directorate (23)
- Computing and Computational Sciences Directorate (35)
- Energy Science and Technology Directorate (217)
- Fusion and Fission Energy and Science Directorate (21)
- Information Technology Services Directorate (2)
- Isotope Science and Enrichment Directorate (6)
- National Security Sciences Directorate (17)
- Neutron Sciences Directorate (11)
- Physical Sciences Directorate
(128)
- User Facilities (27)
Researcher
- Chris Tyler
- Justin West
- Ritin Mathews
- Amit K Naskar
- David Olvera Trejo
- J.R. R Matheson
- Jaswinder Sharma
- Jaydeep Karandikar
- Logan Kearney
- Michael Toomey
- Nihal Kanbargi
- Scott Smith
- Akash Jag Prasad
- Alexander I Wiechert
- Arit Das
- Benjamin L Doughty
- Benjamin Manard
- Brian Gibson
- Brian Post
- Calen Kimmell
- Charles F Weber
- Christopher Bowland
- Costas Tsouris
- Derek Dwyer
- Edgar Lara-Curzio
- Emma Betters
- Felix L Paulauskas
- Frederic Vautard
- Greg Corson
- Holly Humphrey
- Jesse Heineman
- Joanna Mcfarlane
- John Potter
- Jonathan Willocks
- Josh B Harbin
- Louise G Evans
- Matt Vick
- Mengdawn Cheng
- Paula Cable-Dunlap
- Richard L. Reed
- Robert E Norris Jr
- Santanu Roy
- Sumit Gupta
- Tony L Schmitz
- Uvinduni Premadasa
- Vandana Rallabandi
- Vera Bocharova
- Vladimir Orlyanchik
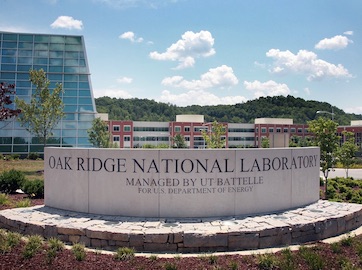
Efficient thermal management in polymers is essential for developing lightweight, high-strength materials with multifunctional capabilities.
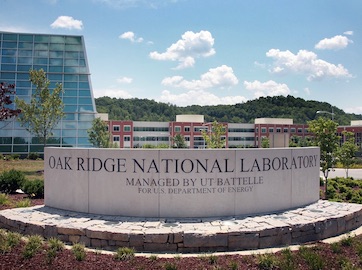
The disclosure is directed to optimized fiber geometries for use in carbon fiber reinforced polymers with increased compressive strength per unit cost. The disclosed fiber geometries reduce the material processing costs as well as increase the compressive strength.
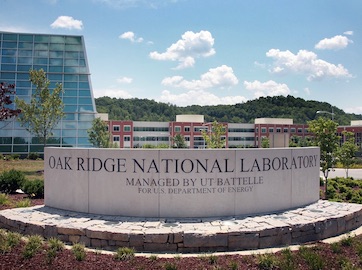
High-gradient magnetic filtration (HGMF) is a non-destructive separation technique that captures magnetic constituents from a matrix containing other non-magnetic species. One characteristic that actinide metals share across much of the group is that they are magnetic.
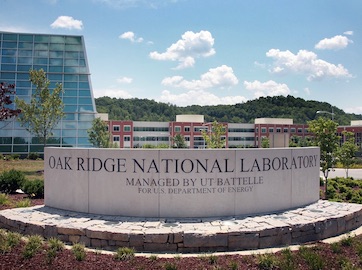
System and method for part porosity monitoring of additively manufactured components using machining
In additive manufacturing, choice of process parameters for a given material and geometry can result in porosities in the build volume, which can result in scrap.
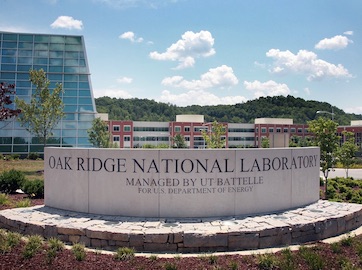
A novel and cost-effective process for the activation of carbon fibers was established.
Contact
To learn more about this technology, email partnerships@ornl.gov or call 865-574-1051.
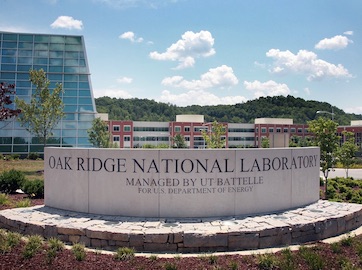
Distortion generated during additive manufacturing of metallic components affect the build as well as the baseplate geometries. These distortions are significant enough to disqualify components for functional purposes.
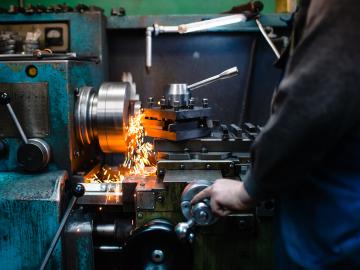
For additive manufacturing of large-scale parts, significant distortion can result from residual stresses during deposition and cooling. This can result in part scraps if the final part geometry is not contained in the additively manufactured preform.
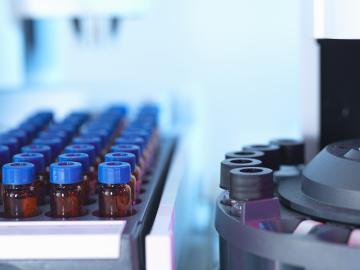
Pyrolysis evolved gas analysis – mass spectrometry (EGA-MS) and pyrolysis gas chromatography – MS (GC-MS) – are powerful analytical tools for polymer characterization.
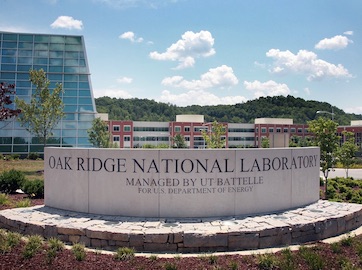
In additive manufacturing large stresses are induced in the build plate and part interface. A result of these stresses are deformations in the build plate and final component.