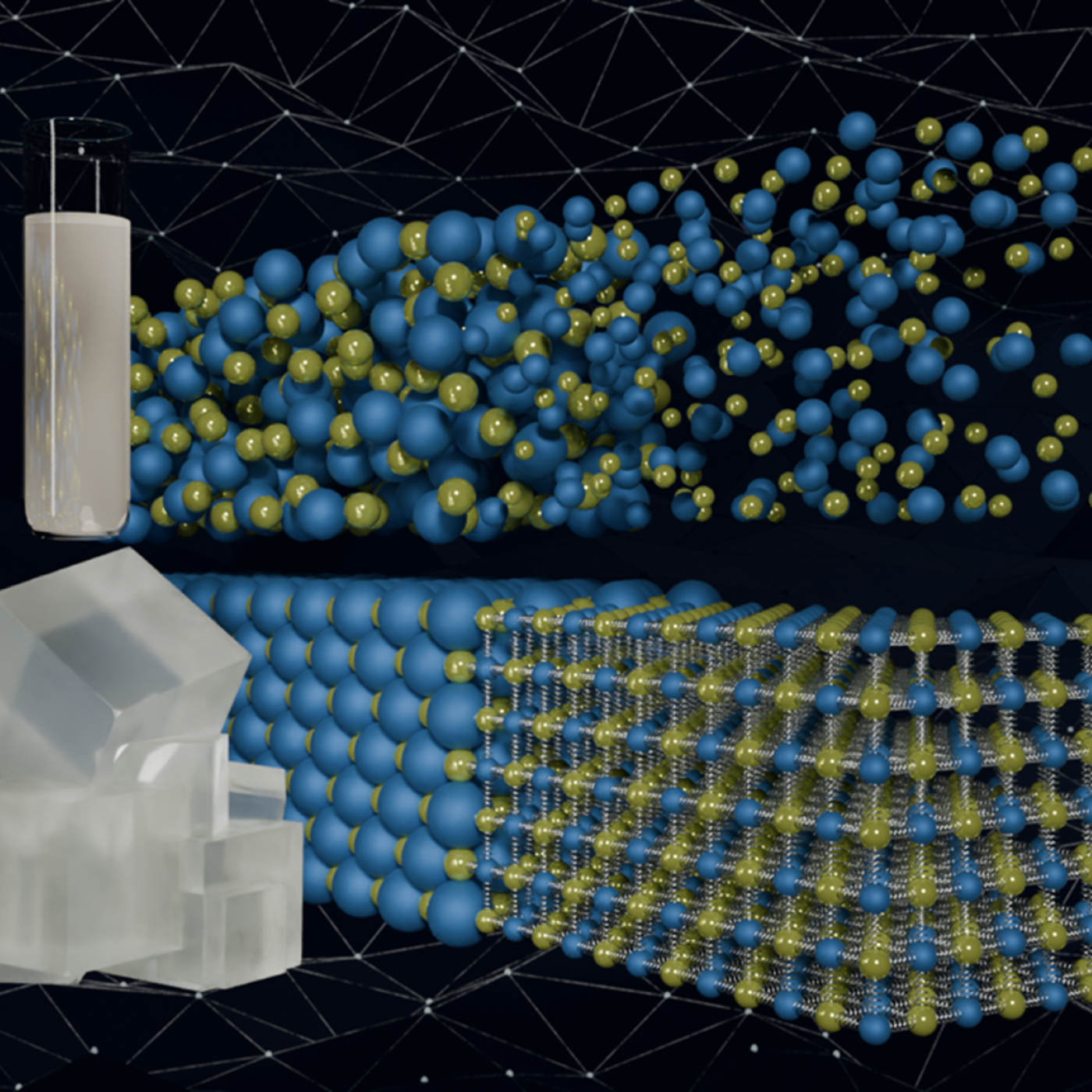
Filter News
Area of Research
- Advanced Manufacturing (22)
- Biology and Environment (30)
- Building Technologies (1)
- Computational Engineering (1)
- Computer Science (12)
- Electricity and Smart Grid (3)
- Energy Science (169)
- Energy Sciences (1)
- Functional Materials for Energy (2)
- Fusion and Fission (7)
- Fusion Energy (1)
- Isotopes (1)
- Materials (69)
- Materials for Computing (10)
- National Security (24)
- Neutron Science (21)
- Nuclear Science and Technology (4)
- Quantum information Science (9)
- Sensors and Controls (1)
- Supercomputing (64)
News Topics
- (-) 3-D Printing/Advanced Manufacturing (146)
- (-) Big Data (79)
- (-) Energy Storage (114)
- (-) Grid (74)
- (-) Machine Learning (68)
- (-) Quantum Science (92)
- Advanced Reactors (40)
- Artificial Intelligence (131)
- Bioenergy (112)
- Biology (128)
- Biomedical (73)
- Biotechnology (39)
- Buildings (74)
- Chemical Sciences (86)
- Clean Water (33)
- Composites (35)
- Computer Science (226)
- Coronavirus (48)
- Critical Materials (29)
- Cybersecurity (35)
- Education (5)
- Element Discovery (1)
- Emergency (4)
- Environment (218)
- Exascale Computing (67)
- Fossil Energy (8)
- Frontier (64)
- Fusion (66)
- High-Performance Computing (130)
- Hydropower (12)
- Irradiation (3)
- Isotopes (62)
- ITER (9)
- Materials (157)
- Materials Science (158)
- Mathematics (12)
- Mercury (12)
- Microelectronics (4)
- Microscopy (56)
- Molten Salt (10)
- Nanotechnology (64)
- National Security (86)
- Neutron Science (171)
- Nuclear Energy (122)
- Partnerships (68)
- Physics (69)
- Polymers (35)
- Quantum Computing (53)
- Security (31)
- Simulation (65)
- Software (1)
- Space Exploration (26)
- Statistics (4)
- Summit (71)
- Transportation (103)
Media Contacts
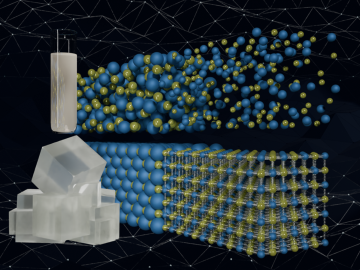
Scientists have developed a new machine learning approach that accurately predicted critical and difficult-to-compute properties of molten salts, materials with diverse nuclear energy applications.

From decoding plant genomes to modeling microbial behavior, computational biologist Priya Ranjan builds computational tools that turn extensive biological datasets into real-world insights. These tools transform the way scientists ask and answer complex biological questions that advance biotechnology breakthroughs and support cultivation of better crops for energy and food security.
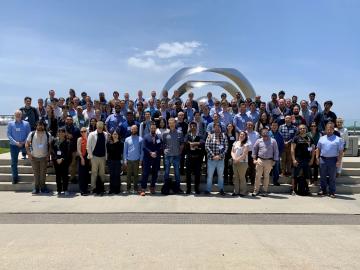
Members of the Quantum Science Center, or QSC, gathered at an all-hands meeting in Baton Rouge, Louisiana, in mid-May to reflect on the remarkable accomplishments from the past five years and to prepare for what members hope to be the next five years of the center.

Recent advancements at ORNL show that 3D-printed metal molds offer a faster, more cost-effective and flexible approach to producing large composite components for mass-produced vehicles than traditional tooling methods.
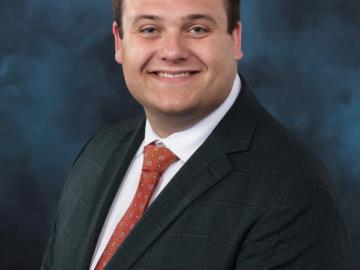
Paul is exploring the next frontier: bridging quantum computing with neutron science. His research aims to integrate quantum algorithms with neutron scattering experiments, opening new possibilities for understanding materials at an atomic level.
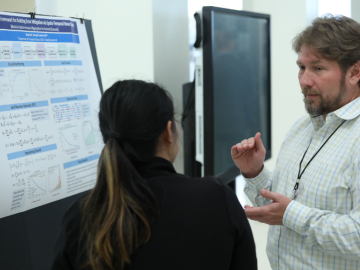
The fifth annual Quantum Science Center, or QSC, Summer School at Purdue University, held Apr. 21 through Apr. 25, 2025, welcomed its largest group of students to date. Experts from industry, academia and national laboratories gathered at the Purdue Quantum Science and Engineering Institute to share their research in multiple areas of quantum science.
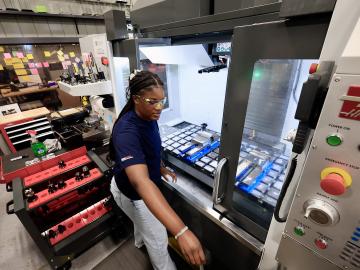
UT-Battelle has contributed up to $475,000 for the purchase and installation of advanced manufacturing equipment to support a program at Tennessee’s Oak Ridge High School that gives students direct experience with the AI- and robotics-assisted workplace of the future.
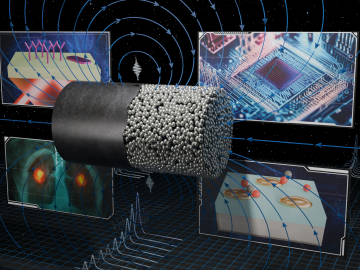
A research team from the Department of Energy’s Oak Ridge National Laboratory, in collaboration with North Carolina State University, has developed a simulation capable of predicting how tens of thousands of electrons move in materials in real time, or natural time rather than compute time.
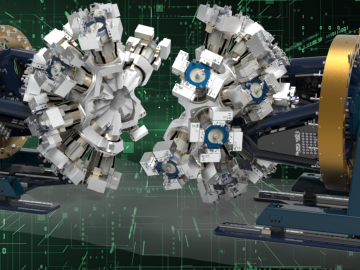
Analyzing massive datasets from nuclear physics experiments can take hours or days to process, but researchers are working to radically reduce that time to mere seconds using special software being developed at the Department of Energy’s Lawrence Berkeley and Oak Ridge national laboratories.
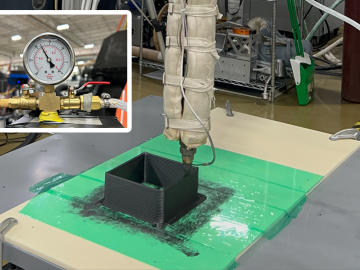
Scientists at ORNL have developed a vacuum-assisted extrusion method that reduces internal porosity by up to 75% in large-scale 3D-printed polymer parts. This new technique addresses the critical issue of porosity in large-scale prints but also paves the way for stronger composites.