Filter News
Area of Research
News Topics
- (-) Composites (11)
- (-) Materials Science (26)
- 3-D Printing/Advanced Manufacturing (30)
- Advanced Reactors (5)
- Artificial Intelligence (45)
- Big Data (28)
- Bioenergy (16)
- Biology (22)
- Biomedical (13)
- Biotechnology (10)
- Buildings (29)
- Chemical Sciences (30)
- Clean Water (6)
- Computer Science (46)
- Critical Materials (7)
- Education (2)
- Emergency (3)
- Energy Storage (15)
- Environment (38)
- Exascale Computing (25)
- Fossil Energy (4)
- Frontier (21)
- Fusion (12)
- Grid (16)
- High-Performance Computing (45)
- Hydropower (1)
- Isotopes (17)
- ITER (2)
- Machine Learning (23)
- Materials (24)
- Mathematics (7)
- Microelectronics (2)
- Microscopy (4)
- Molten Salt (1)
- Nanotechnology (2)
- National Security (34)
- Neutron Science (23)
- Nuclear Energy (15)
- Partnerships (29)
- Physics (9)
- Polymers (5)
- Quantum Computing (20)
- Quantum Science (22)
- Security (8)
- Simulation (24)
- Space Exploration (3)
- Statistics (3)
- Summit (14)
- Transportation (15)
ORNL's Communications team works with news media seeking information about the laboratory. Media may use the resources listed below or send questions to news@ornl.gov.
1 - 10 of 33 Results

ORNL researchers created and tested two methods for transforming coal into the scarce mineral graphite, which is used in batteries for electric vehicles.
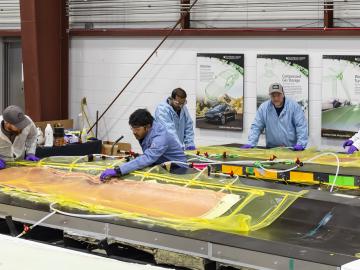
ORNL researchers reached a significant milestone by building an entire 6.5-foot turbine blade tip using novel materials. The team then tested it against the forces of simulated lightning in a specialized lab at Mississippi State University, where the blade tip emerged pristine after tests that isolate the effects of high voltage.
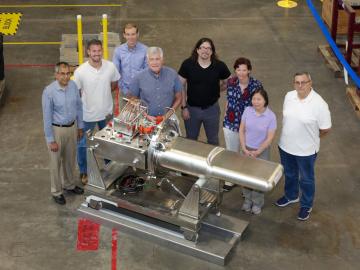
The Proton Power Upgrade project at ORNL's Spallation Neutron Source has achieved its final key performance parameter of 1,250 hours of neutron production at 1.7 megawatts of proton beam power on a newly developed target.
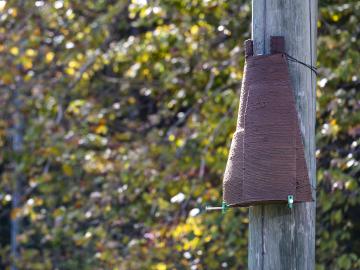
Oak Ridge National Laboratory researchers are using a new bioderived material to 3D print custom roosting structures for endangered bats.

Biochemist David Baker — just announced as a recipient of the Nobel Prize for Chemistry — turned to the High Flux Isotope Reactor (HFIR) at Oak Ridge National Laboratory for information he couldn’t get anywhere else. HFIR is the strongest reactor-based neutron source in the United States.
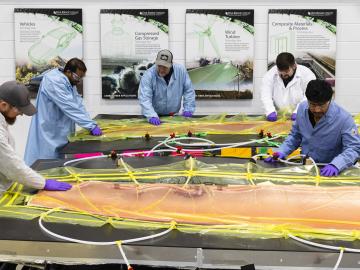
ORNL researchers were honored with a prestigious ACE Award for Composites Excellence by the American Composites Manufacturers Association. The team won the “innovation in green composites design” prize for creating a fully recyclable, lightweight wind turbine blade tip that incorporates low-cost carbon fiber and conductive coating for enhanced protection against lightning strikes.
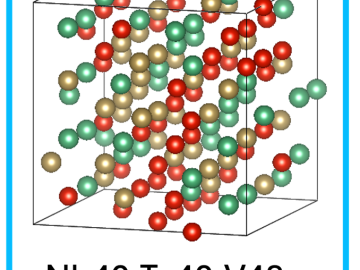
A study led by the Department of Energy’s Oak Ridge National Laboratory details how artificial intelligence researchers created an AI model to help identify new alloys used as shielding for housing fusion applications components in a nuclear reactor. The findings mark a major step towards improving nuclear fusion facilities.
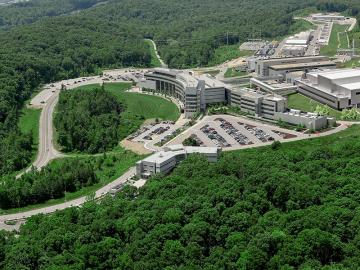
ORNL's Spallation Neutron Source, the nation’s leading source of pulsed neutron beams for research, was recently restarted after nine months of upgrade work.
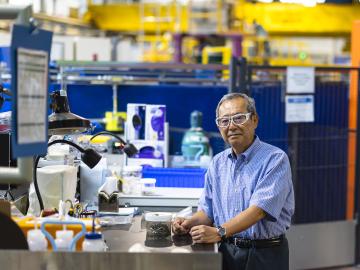
Distinguished materials scientist Takeshi Egami has spent his career revealing the complex atomic structure of metallic glass and other liquids — sometimes sharing theories with initially resistant minds in the scientific community.
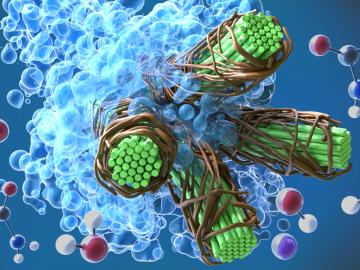
A team led by scientists at ORNL identified and demonstrated a method to process a plant-based material called nanocellulose that reduced energy needs by a whopping 21%, using simulations on the lab’s supercomputers and follow-on analysis.