Filter Results
Related Organization
- Biological and Environmental Systems Science Directorate (29)
- Computing and Computational Sciences Directorate (39)
- Energy Science and Technology Directorate (229)
- Fusion and Fission Energy and Science Directorate
(24)
- Information Technology Services Directorate (3)
- Isotope Science and Enrichment Directorate (7)
- National Security Sciences Directorate (20)
- Neutron Sciences Directorate (11)
- Physical Sciences Directorate (138)
- User Facilities
(28)
Researcher
- Costas Tsouris
- Eddie Lopez Honorato
- Ryan Heldt
- Tyler Gerczak
- Vincent Paquit
- Akash Jag Prasad
- Bogdan Dryzhakov
- Calen Kimmell
- Callie Goetz
- Canhai Lai
- Christopher Hobbs
- Christopher Rouleau
- Chris Tyler
- Clay Leach
- Fred List III
- Gs Jung
- Gyoung Gug Jang
- Ilia N Ivanov
- Ivan Vlassiouk
- James Haley
- James Parks II
- Jaydeep Karandikar
- Jong K Keum
- Keith Carver
- Kyle Kelley
- Matt Kurley III
- Mina Yoon
- Radu Custelcean
- Richard Howard
- Rodney D Hunt
- Ryan Dehoff
- Steven Randolph
- Thomas Butcher
- Vladimir Orlyanchik
- Zackary Snow
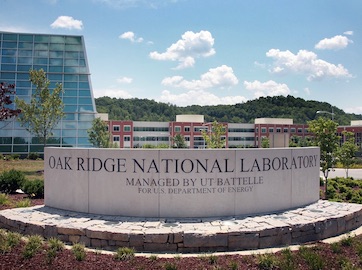
System and method for part porosity monitoring of additively manufactured components using machining
In additive manufacturing, choice of process parameters for a given material and geometry can result in porosities in the build volume, which can result in scrap.
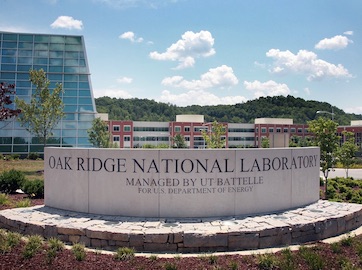
A pressure burst feature has been designed and demonstrated for relieving potentially hazardous excess pressure within irradiation capsules used in the ORNL High Flux Isotope Reactor (HFIR).
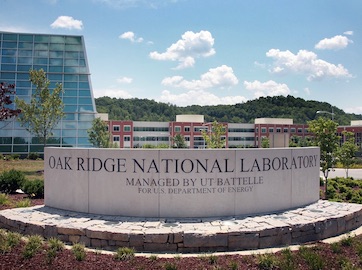
Sintering additives to improve densification and microstructure control of UN provides a facile approach to producing high quality nuclear fuels.
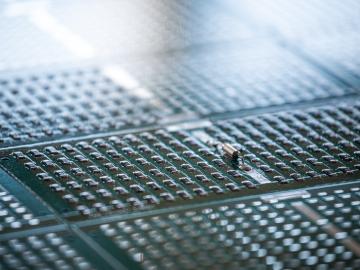
High coercive fields prevalent in wurtzite ferroelectrics present a significant challenge, as they hinder efficient polarization switching, which is essential for microelectronic applications.
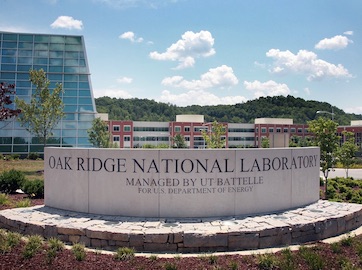
Sensing of additive manufacturing processes promises to facilitate detailed quality inspection at scales that have seldom been seen in traditional manufacturing processes.
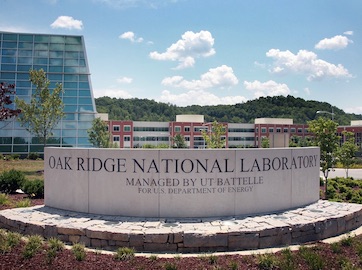
This technology is a laser-based heating unit that offers rapid heating profiles on a research scale with minimal incidental heating of materials processing environments.
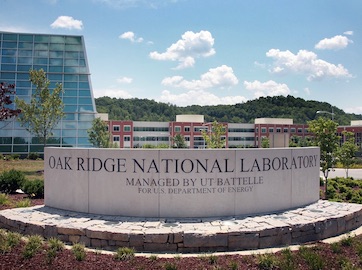
In order to avoid the limitations and costs due to the use of monolithic components for chemical vapor deposition, we developed a modular system in which the reaction chamber can be composed of a top and bottom cone, nozzle, and in-situ reaction chambers.
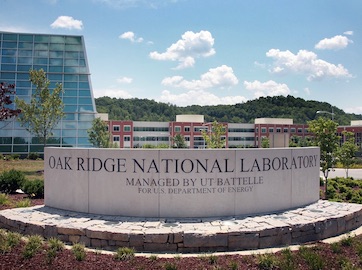
The use of Fluidized Bed Chemical Vapor Deposition to coat particles or fibers is inherently slow and capital intensive, as it requires constant modifications to the equipment to account for changes in the characteristics of the substrates to be coated.
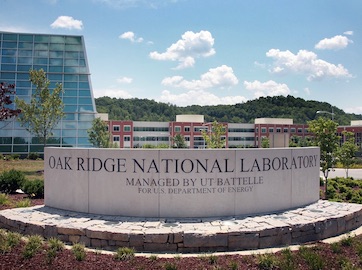
A novel molecular sorbent system for low energy CO2 regeneration is developed by employing CO2-responsive molecules and salt in aqueous media where a precipitating CO2--salt fractal network is formed, resulting in solid-phase formation and sedimentation.