Magnum Venus Products (MVP), in partnership with Oak Ridge National Laboratory (ORNL), recently celebrated the installation of the first commercially available medium/large-scale thermoset 3D printer at the Department of Energy’s Manufacturing Demonstration Facility at ORNL. MVP and ORNL hosted a a ribbon-cutting ceremony on April 5, 2018.
While 3D printers have been around for years, the additive manufacturing industry has needed a cost-effective solution that could print structures and molds. MVP engaged with ORNL to create this 3D printer capable of printing large-scale thermosets, chemistries that are irreversibly cured from a prepolymer or resin.
The MVP machine features a state-of-the-art gantry system tailored to the application, developed in response to growth in 3D printing, a market demand for hyper-customization, and the need for advanced manufacturing automation. The ability to print thermosets on a large-scale opens new possibilities with respect to the performance and integrity of printed structures.
The roll-in/roll-out bed configuration of the MVP thermoset printer dramatically increases the productivity of additive manufacturing. The configuration allows the printer to operate while pre- and post-processing operations are performed on an additional print bed outside of the machine. The benefits include rapid prototyping molds, rapid mold building, and creativity with an all-new material for cutting-edge companies. It also includes the ability to print new structures with materials more tailored to strength than traditional thermoplastics.
The printer’s specifications include:
- Multi-axis print head + coordinated control of other print process parameters
- Build volume: 16’ x 8’ x 42’’
- Can print up to 50” per second (depending on material being used)
- Deposition rate ≥ 10 lbs./hr.
- Resolution of ≤ 6mm and larger resolution is possible
- Build platform with 1,000 lb. capacity
- Repeatability = ±0.005”
- Large footprint can be scaled to multiple sizes with ease
“Thanks to this innovation, research and development managers will be able to prototype faster and bring products to market faster,” said Bob Vanderhoff, CEO Magnum Venus Products. “Procurement departments will also enjoy shortened lead time on crucial molds – allowing for rapid deployment. This was made possible through ORNL slicing software that allows the integration of multivariate print process parameters.”
“We’re pleased to collaborate with MVP on this state-of-the-art printer and look forward to seeing the technology continue to progress and positively impact the additive manufacturing industry,” said Moe Khaleel, ORNL Associate Laboratory Director for Energy and Environmental Sciences. “This collaboration is important for accelerating the pace with which new technologies can be successfully commercialized, leading to a larger range of applications and performance criteria for additively manufactured components, while creating new jobs and increased prosperity in our region.”
The Manufacturing Demonstration Facility is supported by the DOE Office of Energy Efficiency and Renewable Energy’s Advanced Manufacturing Office. AMO supports early-stage research to advance innovation in U.S. manufacturing and promote American economic growth and energy security.
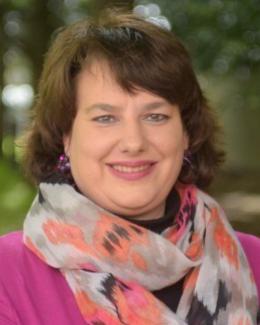