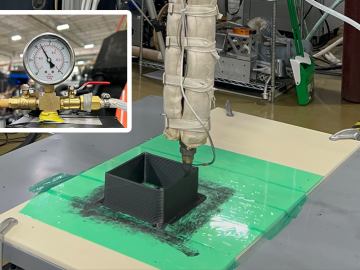
Scientists at ORNL have developed a vacuum-assisted extrusion method that reduces internal porosity by up to 75% in large-scale 3D-printed polymer parts.
Scientists at ORNL have developed a vacuum-assisted extrusion method that reduces internal porosity by up to 75% in large-scale 3D-printed polymer parts.
The University of Oklahoma and Oak Ridge National Laboratory, the Department of Energy’s largest multi-program science and energy laboratory, have entered a strategic collaboration to establish a cutting-edge additive manufacturing center based in Norma
Inspired by a visit to ORNL’s Manufacturing Demonstration Facility, Jonaaron Jones launched a career in additive manufacturing that led to founding Volunteer Aerospace and now leading Beehive Industries’ external parts business.
During his first visit to Oak Ridge National Laboratory, Energy Secretary Chris Wright compared the urgency of the Lab’s World War II beginnings to today’s global race to lead in artificial intelligence, calling for a “Manhattan Project 2.”
The presence of minerals called ash in plants makes little difference to the fitness of new naturally derived compound materials designed for additive manufacturing, an Oak Ridge National Laboratory-led team found.
A new deep-learning framework developed at ORNL is speeding up the process of inspecting additively manufactured metal parts using X-ray computed tomography, or CT, while increasing the accuracy of the results.
When Andrew Sutton arrived at ORNL in late 2020, he knew the move would be significant in more ways than just a change in location.
Oak Ridge National Laboratory researchers recently used large-scale additive manufacturing with metal to produce a full-strength steel component for a wind turbine, proving the technique as a viable alternative to
A novel method to 3D print components for nuclear reactors, developed by the Department of Energy’s Oak Ridge National Laboratory, has been licensed by Ultra Safe Nuclear Corporation.