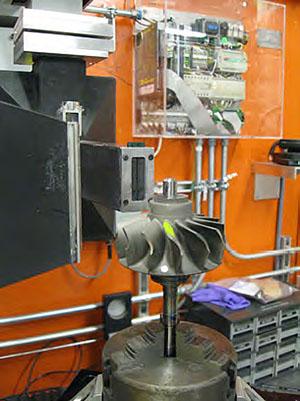
ORNL’s Residual Stress User Center, a joint effort of the High Temperature Materials Laboratory and the Neutron Sciences Directorate, conducts nondestructive testing of engine com¬ponents using neutron and x-ray diffraction techniques. These techniques help industry partners identify manufacturing processes that minimize the generation of residual stresses, test whether a part can tolerate demanding applications, and see whether heat treatment (e.g., annealing) can eliminate or reduce residual stresses in a component. Developers of computer models can incorporate data from these studies to predict more accurately when residual stresses combined with external stresses will cause deterioration and failure. Researchers from Honeywell Turbo Technologies used neutron and x-ray diffraction instruments available through the Center to measure residual stresses in shaft wheel assembly (SWA) weld joints from vehicle turbochargers produced under different conditions.
For more information, please contact Edgar Lara-Curzio, laracurzioe@ornl.gov.