A partnership of the US Department of Energy’s (DOE) Oak Ridge National Laboratory (ORNL), National Renewable Energy Laboratory (NREL), Sandia National Laboratories, and private company TPI Composites recently demonstrated the significant time and cost savings potential of using additive manufacturing techniques in the construction of wind turbine blades.
Researchers examined how additive manufacturing could be used in wind blade mold fabrication to decrease lead time and costs, leveraging technology at the DOE Manufacturing Demonstration Facility (MDF) at ORNL.
The traditional process to create a wind blade mold involves creating a physical model, or plug, of the blade; coating it with fiberglass to create a mold; running miles of wire through the mold to heat it and cure the resins; and making final adjustments to ensure the mold is within specification.
The entire tooling process can take months, sometimes up to a year, and can cost anywhere from hundreds of thousands to a million dollars for each blade. Blades are one of the most expensive components of wind turbines, and that cost is rising with the demand for larger blade sizes.
By pursuing direct printing of the molds, researchers targeted greater efficiency and cost savings as part of DOE’s commitment to improve the competitiveness of US manufacturers. Additive manufacturing eliminates the need for the plug, and by building ducts into the mold’s design, manufacturers could use hot air to cure the mold’s fiberglass finish, eliminating the need for wiring.
Sandia National Laboratories designed the blade for the project. ORNL then designed, printed, and finished the mold at the MDF facility. Arizona-based wind blade manufacturer TPI produced three blades from the mold. NREL performed initial testing on the blades at its Colorado facilities, and the blades will undergo further testing at DOE’s Scaled Wind Farm Technology facility in Texas.
“The process reduces the time to manufacture the molds by reducing complexity. We demonstrated that the process could be accomplished in weeks rather than months, with costs projected at far less,” said Lonnie Love, Corporate Fellow researcher and leader of the Manufacturing Systems Research group at ORNL.
Research and design for the first-of-its kind project took a few months ahead of the actual printing, Love noted, including designing the ducts to accommodate the passage of air through the mold. Afterward, printing the mold took a few weeks.
Making the mold
ORNL researchers printed the mold at the MDF using Cincinnati Incorporated’s Big-Area Additive Manufacturing (BAAM) platform at ORNL. BAAM can accommodate the creation of objects 20 ft. long, 8 ft. wide, and 6 ft. tall, and it deposits about 100 lb./hour of material. The blade mold, at 13 meters (roughly 50 ft.) long, was printed in 8 sections of about 6 ft. each.
ORNL used ABS polymer reinforced with 20% carbon fiber by volume. The material is the “workhorse” for ORNL’s additive manufacturing research and typically costs about $4–$5/lb., Love said. He noted that other materials such as glass fiber could cut those costs in half. The lab has been researching the use of biobased materials such as bamboo and other wood composites in additive manufacturing as well—an advancement that would deepen the sustainable aspects of wind generation.
After printing, the mold was coated with fiberglass. During the hot-air curing process, researchers made an interesting discovery. While they had been expecting the mold to expand over its length during the finishing process, they found no expansion of the material at all. The long fibers within the coating stabilized the part instead, Love said. The ORNL engineers are leveraging that knowledge as they continue to research large-scale additive manufacturing.
The use of a printing platform with a larger area would reduce manufacturing time and costs even more, Love explained. ORNL is working with Ingersoll Machine Tools to develop a new Wide and High Additive Manufacturing, or WHAM machine. WHAM will be able to accommodate objects as large as 100 ft. long, 25 ft. wide, and 20 ft. tall, depositing some 1,000 lb./hour of material. With such a machine, the blade molds could be printed in a matter of days, Love said.
Reducing the cost of blade molds can also encourage more creativity in blade design. “It was one of our main motivations in the project,” he noted. Having that flexibility can in turn improve the efficiency of a wind farm, for instance.
More blade designs = more efficiency
Researchers have hypothesized that the efficiency of a wind turbine field could be improved if blades of different designs could be installed in different areas of the field in response to changing air patterns. However, the cost of creating additional molds to produce those blades has been prohibitive to date.
Another question to explore is whether wind blade production could be moved closer to the wind farms, or somehow made mobile. Transporting the enormous blades from factories to wind fields can make up as much as 20% of the final cost of the turbines and towers.
“We achieved our objective, delivered what we were asked to deliver, and now these blades are going into the testing phase. They’re like the blades on any other wind turbine out there—just made differently,” Love said. The labs are “at the leading edge of the research, and that’s just where we want to be. Out front, and letting others follow and commercialize these techniques.”
“This idea of being able to make big things fast and inexpensively is pretty important,” said Bill Peter, director of the MDF at ORNL. “Reducing tooling costs so you can have more customizable blades has a lot of potential” to make wind generation more efficient and to boost the prospects for both a domestic energy source and a thriving domestic manufacturing sector.
DOE’s Wind Energy Technologies and Advanced Manufacturing offices, both part of the agency’s Office of Energy Efficiency and Renewable Energy, co-sponsored the project. —by Stephanie Seay
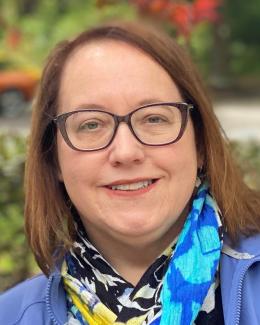