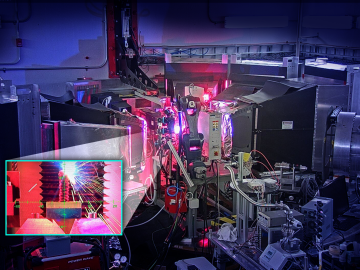
Using neutrons to see the additive manufacturing process at the atomic level, scientists have shown that they can measure strain in a material as it evolves and track how atoms move in response to stress.
Using neutrons to see the additive manufacturing process at the atomic level, scientists have shown that they can measure strain in a material as it evolves and track how atoms move in response to stress.
As current courses through a battery, its materials erode over time. Mechanical influences such as stress and strain affect this trajectory, although their impacts on battery efficacy and longevity are not fully understood.
Stan David, retired scientist and Corporate Fellow Emeritus at the Department of Energy’s Oak Ridge National Laboratory, was awarded the Joining and Welding Science Award from the Joining and Welding Research Institute at Osaka University, Japan.
ORNL researchers have identified a mechanism in a 3D-printed alloy – termed “load shuffling” — that could enable the design of better-performing lightweight materials for vehicles.
The U.S. Departments of Energy and Defense teamed up to create a series of weld filler materials that could dramatically improve high-strength steel repair in vehicles, bridges and pipelines.
The Department of Energy’s Oak Ridge National Laboratory has exclusively licensed battery electrolyte technology to Safire Technology Group.
ORNL scientists will present new technologies available for licensing during the annual Technology Innovation Showcase. The event is 9 a.m. to 3 p.m. Thursday, June 16, at the Manufacturing Demonstration Facility at ORNL’s Hardin Valley campus.
A multidisciplinary team of scientists at ORNL has applied a laser-interference structuring, or LIS, technique that makes significant strides toward eliminating the need for hazardous chemicals in corrosion protection for vehicles.
A new method to produce large, monolayer single-crystal-like graphene films more than a foot long relies on harnessing a “survival of the fittest” competition among crystals.