Invention Reference Number
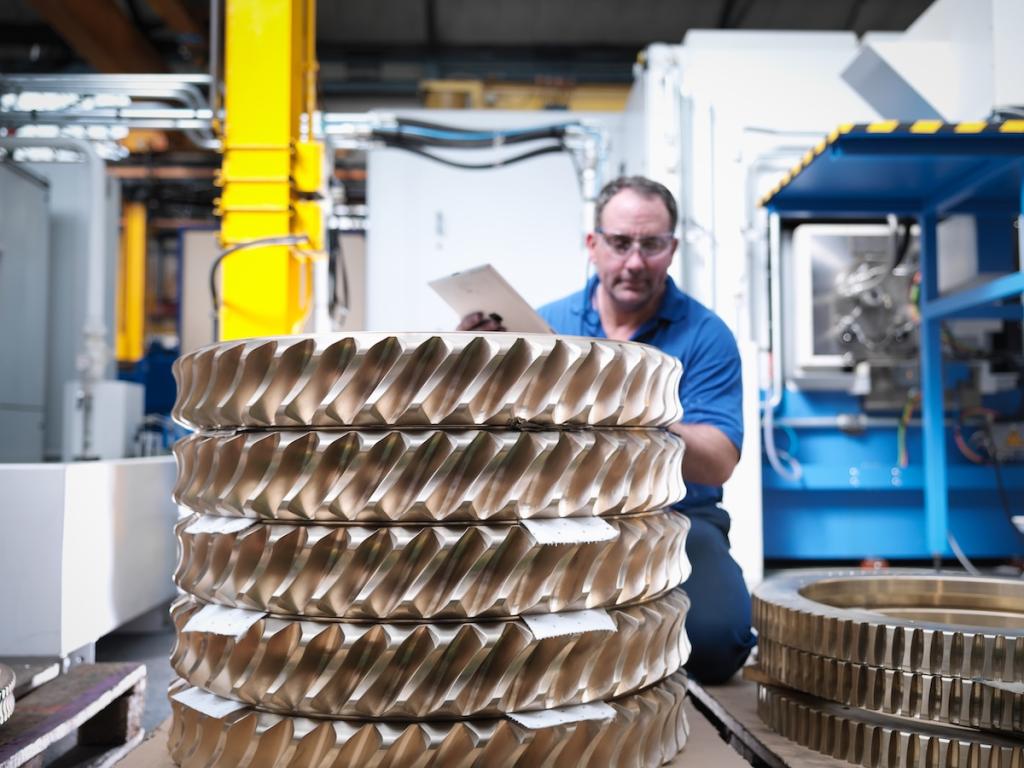
Oak Ridge National Laboratory has developed a novel mechanical correction method to address thermal distortion in Wire Arc Additive Manufacturing (WAAM). This approach reduces warping in printed components by applying targeted compressive force, improving part accuracy and reliability. The technology supports the broader adoption of WAAM in industrial applications where dimensional stability is critical.
Description
WAAM uses heat to deposit metal layer by layer, but the process often generates residual stresses that lead to distortion – especially in large or slender builds. ORNL’s solution involves introducing periodic mechanical compressions along the deposited structure to counteract this deformation. Using a modified tool to apply force at controlled locations, this method reshapes the part without altering the build process or requiring structural changes to the manufacturing platform. A geometric model helps guide compression placement based on observed curvature. This correction technique is adaptable to various part designs and can be integrated into hybrid or automated systems. The result is a practical, scalable solution for minimizing WAAM-induced distortion during or after printing.
Benefits
- Reduces thermal distortion in metal additive manufacturing
- Improves dimensional accuracy without altering deposition methods
- Compatible with a range of part geometries and systems
Applications and Industries
- Additive manufacturing and large-scale metal printing
- Aerospace, defense, and energy infrastructure components
- Industrial tooling and repair part fabrication
Contact
To learn more about this technology, email partnerships@ornl.gov or call 865-574-1051.