New Materials Improve Efficiency
Oak Ridge National Laboratory’s Lightweight Materials research and development activities focus on the development and validation of advanced materials and manufacturing technologies to significantly reduce light and heavy duty vehicle weight without compromising other attributes such as safety, performance, recyclability, and cost.
Because it takes less energy to accelerate a lighter vehicle, replacing traditional steel components with lightweight materials can directly reduce fuel consumption. It also allows cars to carry advanced emissions control equipment, safety devices, and integrated electronic systems without becoming heavier. Lightweight materials are especially important for improving the efficiency and range of hybrid electric, plug-in hybrid electric, and electric vehicles because they offset the weight of power systems such as batteries and electric motors.
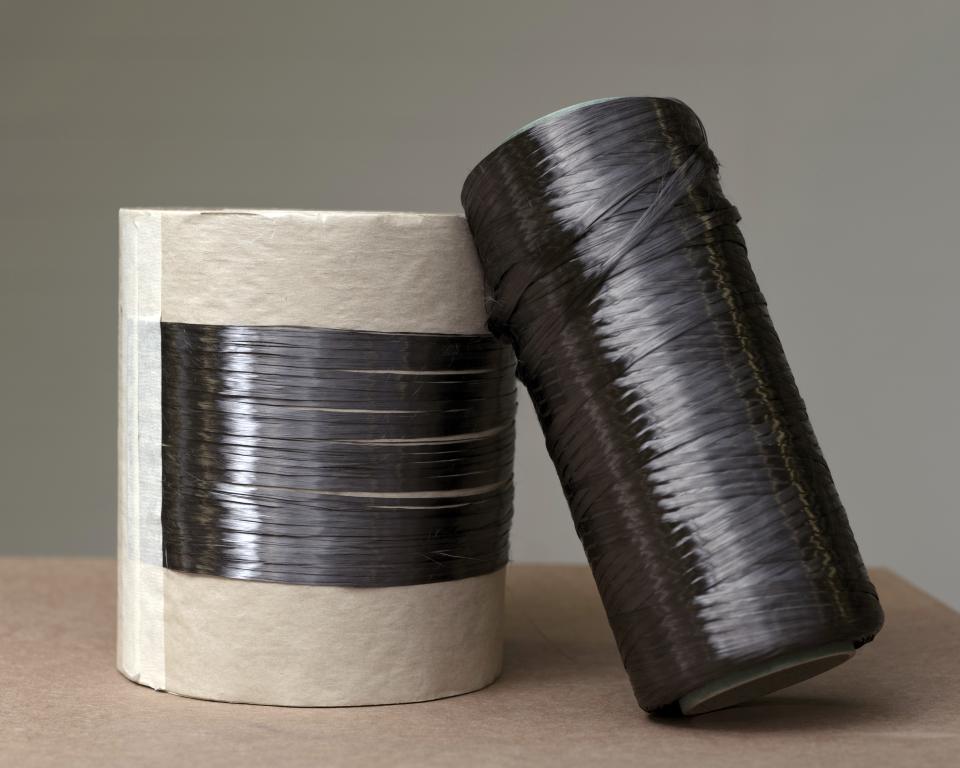
In the short term, vehicle weight reduction can be achieved by replacing heavy steel components with materials such as high-strength steel, aluminum, die cast magnesium or glass fiber polymer composites. In the longer term, wrought magnesium and carbon fiber composites are attractive for greater levels of mass reduction. While the properties of these materials are well established, better and more cost effective technologies and processes are needed for manufacturing, joining, modeling, and recycling. To better understand the properties of these materials and the processes required to maximize their benefits, ORNL conducts lightweight materials research in several areas: materials development, properties and manufacturing, computational materials science, and multi-material enabling. The Department of Energy's (DOE) Vehicle Technologies Officeand industry partners are the primary sponsors of this research.
Materials Development
ORNL is developing lower cost, more environmentally friendly methods for producing carbon fiber and technologies that enable the use of carbon fiber composites, magnesium alloys, advanced high-strength steels and higher-strength aluminum alloys.
ORNL is presently leading a major DOE initiative to develop disruptive technologies for producing low cost carbon fiber. Major focal areas are (i) alternative precursors, (ii) advanced, energy efficient conversion processes, and (iii) scaling for technology transition. ORNL processing capabilities range from single filament to tens of tons annually, with characterization capabilities at length scales from sub-Angstrom to full tows greater than six hundred thousand filaments.
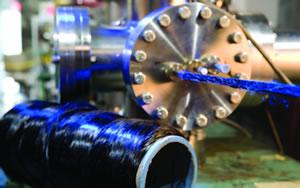
Modeling and Computational Materials Science
ORNL provides supporting technologies such as joining methods, corrosion prevention techniques, and predictive models for full system implementation. Current projects also aid in the development of new, better alloys or composite architectures.
Properties and Manufacturing
Researchers are improving materials properties such as strength, stiffness, and corrosion resistance for a variety of metals and polymer composite materials. Improving manufacturability through increased production rate, ease of materials forming, and greater throughput is another area of focus. Additionally, ORNL is developing robust methods for joining and inspecting similar and dissimilar materials using a variety of processes.
Multi-material Enabling
New methods for reliably joining dissimilar materials are under development along with the necessary inspection techniques and systems analysis to incorporate new materials into future automotive designs.